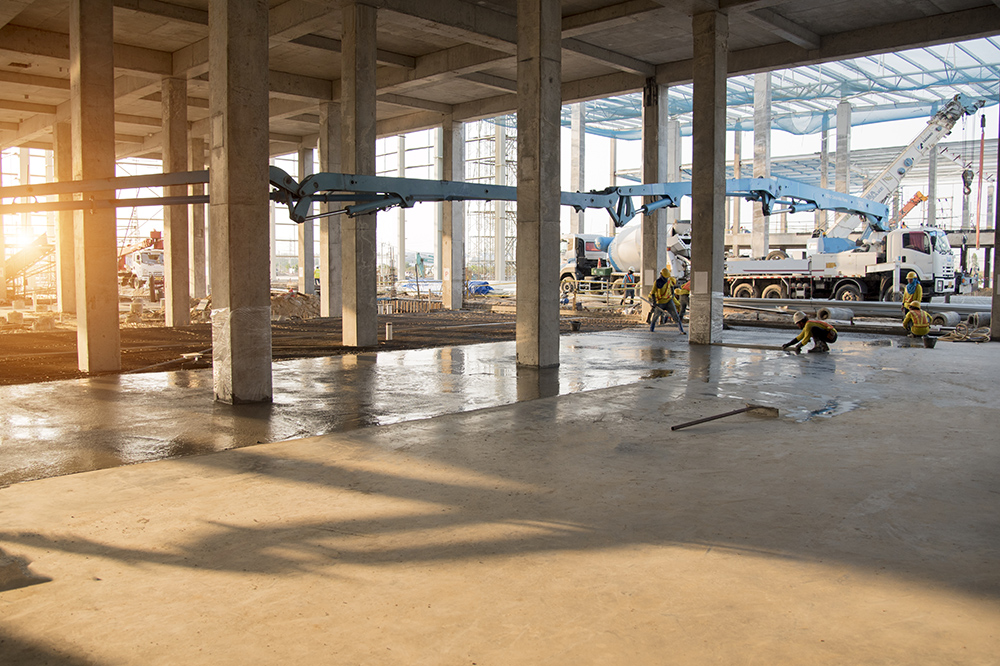
The reinforcement of foundations and walls is an essential part of building construction to ensure the stability and durability of the structure. Traditionally, steel rebars have been used for reinforcement purposes, but the use of composite rebars has gained popularity in recent years due to their various advantages over steel rebars.
Composite rebars are made of a combination of fibers, such as carbon, glass, or basalt, and a polymer resin matrix. They are corrosion-resistant, lightweight, and have a high strength-to-weight ratio, making them an ideal alternative to traditional steel rebars. In addition, composite rebars do not conduct electricity or magnetic fields, making them suitable for use in areas with electromagnetic interference.
One of the significant benefits of using composite rebars for reinforcement is their resistance to corrosion. Steel rebars are prone to corrosion due to the presence of oxygen and moisture, which can lead to structural damage and a shorter lifespan. Composite rebars are non-corrosive, which means they are less likely to deteriorate over time, making them a durable option for reinforcement.
Composite rebars are also lightweight and easy to handle, making them convenient to install in hard-to-reach areas. They can be easily cut and shaped on-site, reducing installation time and labor costs. In addition, composite rebars have a high fatigue resistance, which means they can withstand repeated stress cycles without deteriorating, making them suitable for high-stress applications. With the increasing demand for sustainable and durable building materials, composite rebars are likely to become a more popular choice in the future.